Background
During my bachelor degree in Aeronautical Engineering at The University INHolland, I started working at a company that develops and manufactures composite products for the aerospace industry. I gained hands-on experience in creating products such as door panels, gun turrets, nose cones and manifolds. A variety of production methods were used such as; wet lay-up, RTM injection and pre-preg composite in a high temp/pressure autoclave.
After finishing my degree, I was employed for a fixed period of time as a Computation Fluid Dynamics [CFD] engineer, for the validation and verification of multiple CFD software packages. Here I obtained the knowledge and skillsets to create, setup, analyze and optimize gas and fluid flows. I also developed an understanding for the mistakes that can be made, the problems that can occur and how to prevent them.
After a sabbatical I started my job as a Project and Sales Engineer at DRIE-D. A company leading in the design and development of lubrication free composite bearings. In this function I took on many projects, focused on solving client’s problems regarding advanced moving structures. This gave me the opportunity to design complicated moving mechanisms for the Maritime and Offshore industry.
A huge benefit of working in this position was to be responsible for all the processes within the project scope. I have been involved in the following processes; budgeting, planning, designing, calculating, manufacturing and assembling. During the projects I collaborate closely with the local machine factory responsible for manufacturing steel and plastic components, enabling me to gain knowledge about professional machining, tooling and determining the material tolerances.
All complicated products at the company were designed with the use of CAD software. Giving me the ability to explore and expand my gained experience at the University of Applied Science. Finite Element Analysis [FEA] was used as a verification and validation method for the made calculations. Finally resulting in a well substantiated design.
Some of our clients at DRIE-D were Allseas Engineering, Boskalis, SBM offshore and Damen, all large-scale concerns. Hence, the reliability of the designed systems were of upmost importance as any failure could result in downtime and ending up costing the client´s millions of dollars each day. ISO9001 was implemented to make sure all processes are according the right standard. Most projects were of short term, giving me the opportunity to play a role in all of the processes.
Over the last 12 years I have worked with many CAD suites including Solidworks, Autodesk, ANSYS, OpenFOAM, Catia V5 and worked with companies all over the world. Learning that it doesn´t matter from where you work as long as you stay digitally connected.
Over 6 years ago I started taking on freelance work as this gave me the chance to work at different projects and be active in more areas of engineering. Expand my mind and knowledge. So far I have been blessed with the amount of work and people I have met. I am a punctual, hardworking engineer with a no-nonsense mentality. Ensuring that you get the results you want, when you want them.
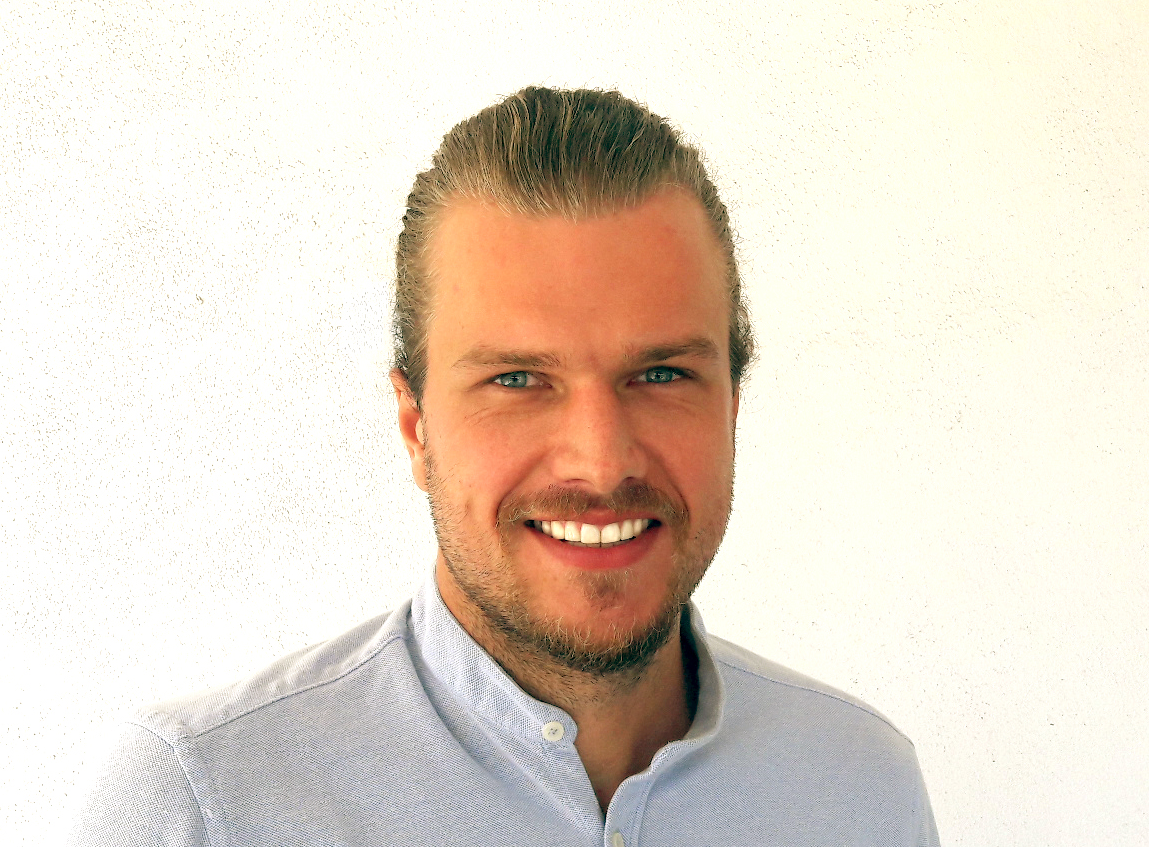
Peter Rupert
Aeronautical Engineer